Breaking tradition, dual-row reactor leads the industrial revolution
In the field of chemical production, dual-row reactors are gradually replacing traditional reactors with their high efficiency, energy saving and intelligent characteristics, becoming a new favorite in industrial production. Recently, the release of a new dual-row reactor system has attracted widespread attention. Its unique design and innovative technology have brought a new solution to chemical production.
Design innovation, efficiency improvement
-
Modular design: This new dual-row reactor adopts a modular design. Each reactor can operate independently or be connected to other reactors through pipelines and valve systems to form a continuous reaction system. The advantage of this design is that the number of reactors can be flexibly adjusted according to production needs, improving production efficiency and flexibility.
-
Automation control: The new dual-row reactor system integrates advanced automation control technology. Each reactor is equipped with an independent control system, which can monitor parameters such as temperature, pressure, pH value in real time, and is uniformly managed through a central control system. This not only improves the stability and safety of the reaction process, but also greatly reduces the error of manual operation.
Wide application prospects
-
Chemical synthesis: In the field of chemical synthesis, the dual reactor system can achieve continuous reaction, improve output and product quality. For example, in drug synthesis, the dual reactor can achieve continuous operation of multi-step reactions, significantly shortening the production cycle .
-
Material science: In the research and development of new materials, the high efficiency and precise control ability of the dual reactor enable researchers to explore and optimize material synthesis conditions more quickly, promoting the rapid development and application of new materials.
-
Environmental engineering: The dual reactor is also widely used in wastewater treatment and environmental remediation. Its modular design and automated control can achieve continuous operation of multiple treatment processes and improve treatment efficiency and effect .
Environmental protection and energy saving
-
Energy saving and emission reduction: The efficient operation and automated control of the dual reactor system help reduce energy consumption and waste emissions, which is in line with the development trend of green chemical industry. For example, in the application of a chemical plant, the new dual-tank reactor system achieved a significant effect of reducing energy consumption by 20% and wastewater discharge by 30%.
-
Resource Utilization: The modular design of the dual-tank reactor facilitates the recycling of resources. For example, the by-products produced during the reaction process can be directly transferred to another reactor for treatment through the dual-tank system, thereby maximizing the utilization of resources and minimizing the discharge of waste.
Conclusion
The launch of the new dual-tank reactor marks that chemical production has entered a new stage of high efficiency, intelligence and environmental protection. Its innovative design and wide application not only improve production efficiency, but also provide new ideas for the development of green chemical industry. In the future, with the continuous advancement and promotion of technology, dual-tank reactors will play an important role in more fields and help the chemical industry achieve sustainable development.
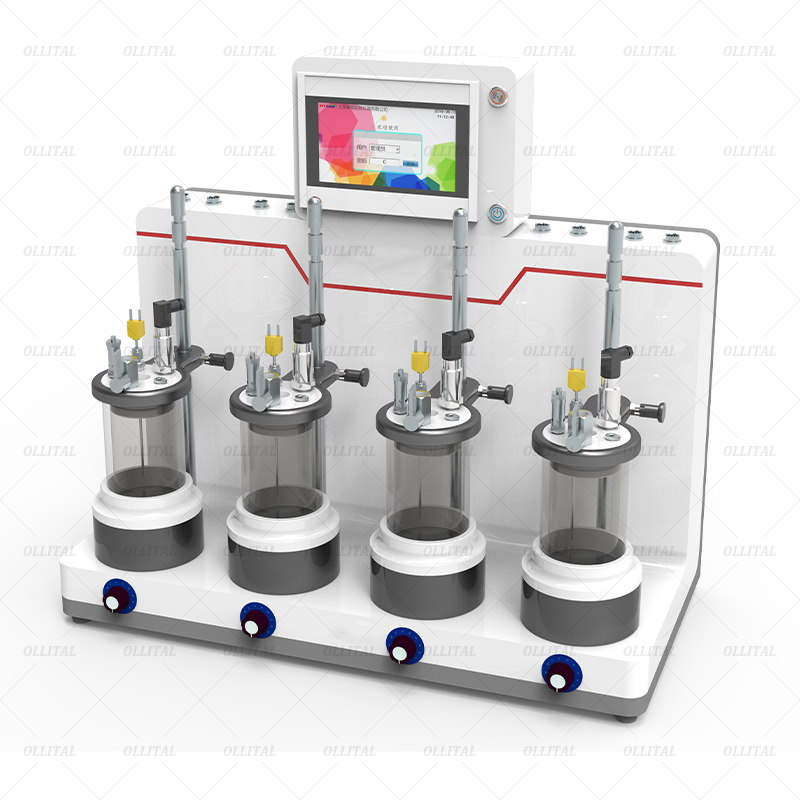